In his story, you can also read about:
- How the blueprint came to Slovakia
- How the patterns differed between regions
-The alchemy of a dying blueprint
-Slovakia's unique contribution to the art of blueprinting
-The story of Matej Rabada, the present-day master blueprinter from Orava
First, carefully spread out metres of plain white fabric on a table to smooth it down. Then apply the pattern, using a wooden form covered in a mushy substance, pressing it onto the fabric as regularly as possible. Bathe the fabric in a large vat of cold indigo blue dye until the indigo oxidizes and permanently colours the cloth.
After about five hours of dyeing, sink the fabric into an acid solution to remove the substance that creates the pattern and fixes the colour. Let it dry, iron well, and your blueprinted fabric is ready.
Even though the blueprint pattern has become popular lately along with everything that is handmade, back-to-roots and folk craft experiencing a revival in fashion, not many people are familiar with how blueprint is produced. Recently, the process entered the UNESCO list of intangible cultural heritage.
“It is the highest appreciation of the work I do and the craft I live from,” Matej Rabada, a blueprinter who continues the traditional hand-made method of fabric production, told The Slovak Spectator.
Blueprinting and its tradition is the sixth Slovak entry on the UNESCO list, nominated within a common candidacy with Germany, Austria, the Czech Republic and Hungary.
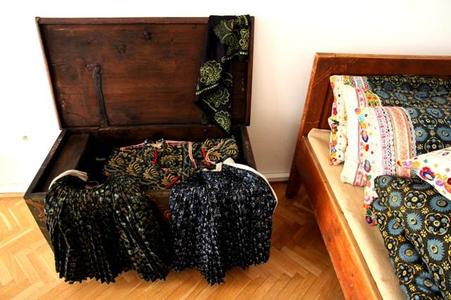
Slovakia has five other features on the world list: